Steady Hands And A Careful Eye
Hand block printing is the earliest, simplest and slowest of all methods of textile printing.
Take a look behind the scenes to see our slow fashion manufacturing in motion.

STEP 1.
Applying Dabu (mud)
Dabu paste is made each morning by the printers. It is made up of black clay, wheat flour, gum and lime water. It is poured into a printing tray which is covered with a wire grill. After each print the block is reloaded with fresh mud to get a clear print each time.
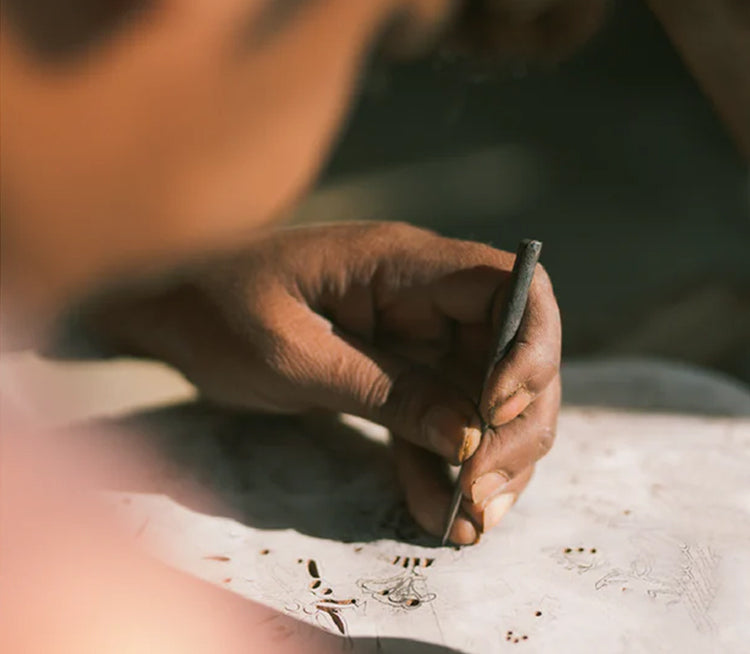
STEP 2.
Block Carving
The block-carving artisans use small hammers, chisels and drills to carve elaborate patterns into wooden blocks.
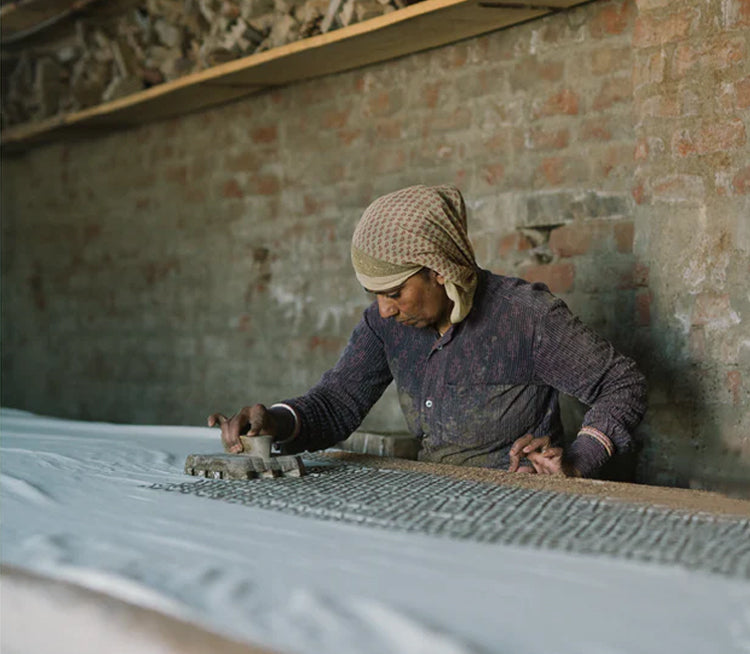
STEP 3.
Printing
Once the block has been placed in the mud, the design is lined up on the fabric and pressed, transferring the mud to the fabric.
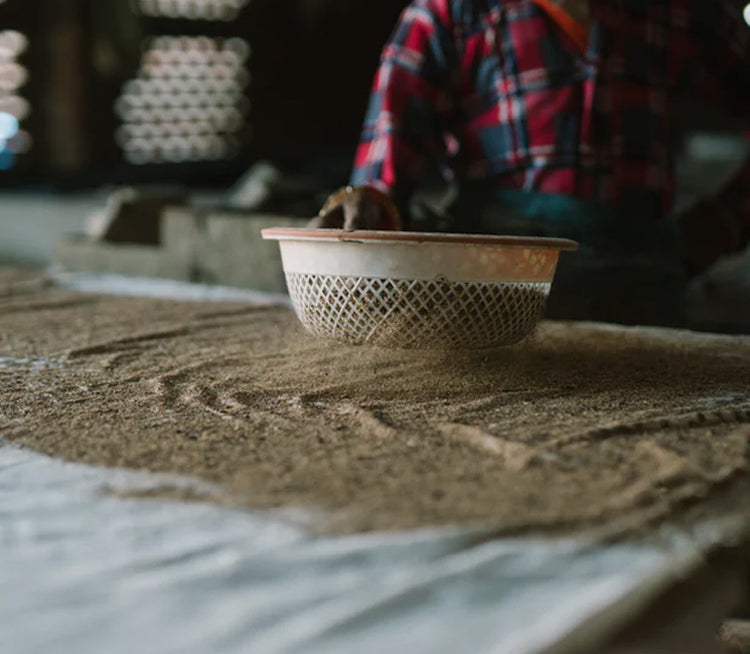
STEP 4.
Sawdust & Drying
Before the mud is dry the fabric must be covered in sawdust. The sawdust binds with the mud to create a strong resistance which will stop the dye from penetrating through. The Dabu printed fabric is then left to dry in the Indian sun. The fabric is carefully washed to remove any dirt, ensuring the mud paste is not removed. The fabric will absorb the dye better after it has been washed.
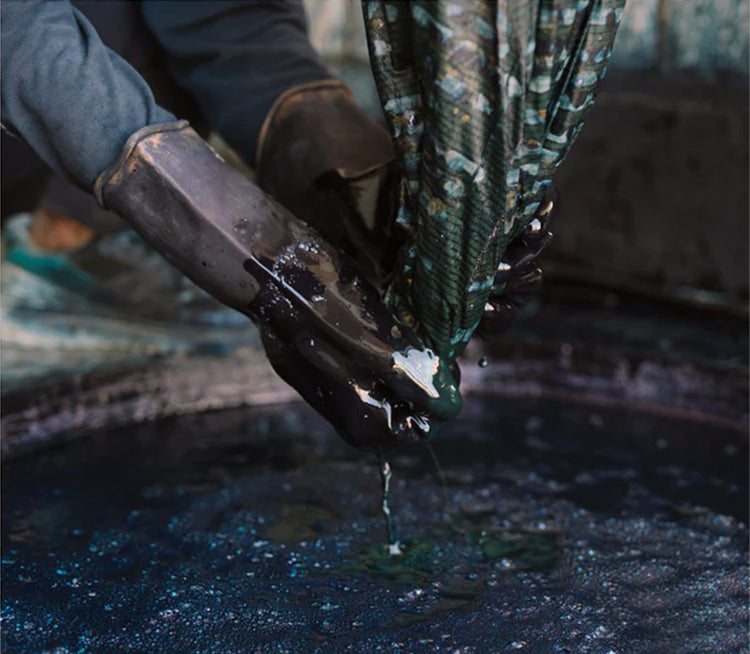
STEP 5.
Dying & Drying
The fabric is lowered into the dying well and left for several minutes so the fabric can absorb the natural dye. It is then dipped again three to four times to increase the depth of colour. It then dries in the sun whilst the colour develops.
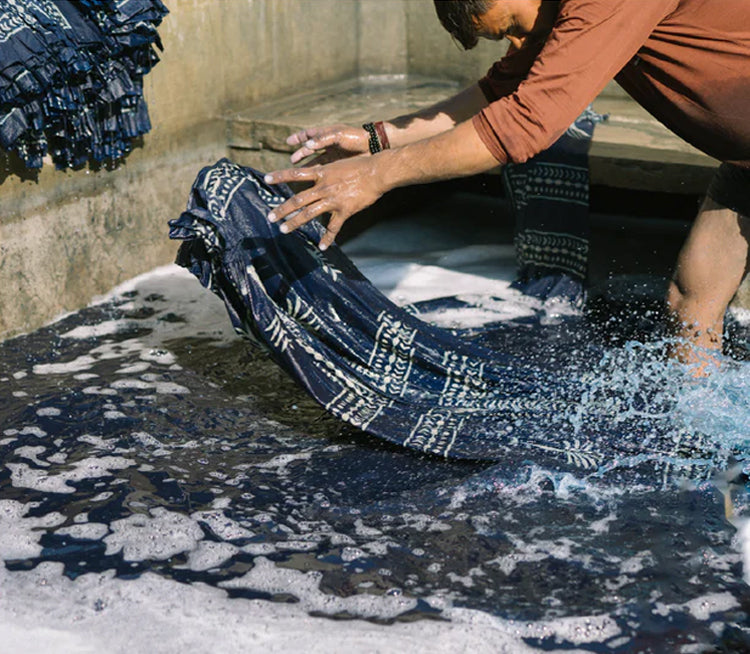
STEP 6.
Washing
Once the colour has fully developed the fabric is then washed to remove any excess dye. After washing it is sent to the drying fields one last time.